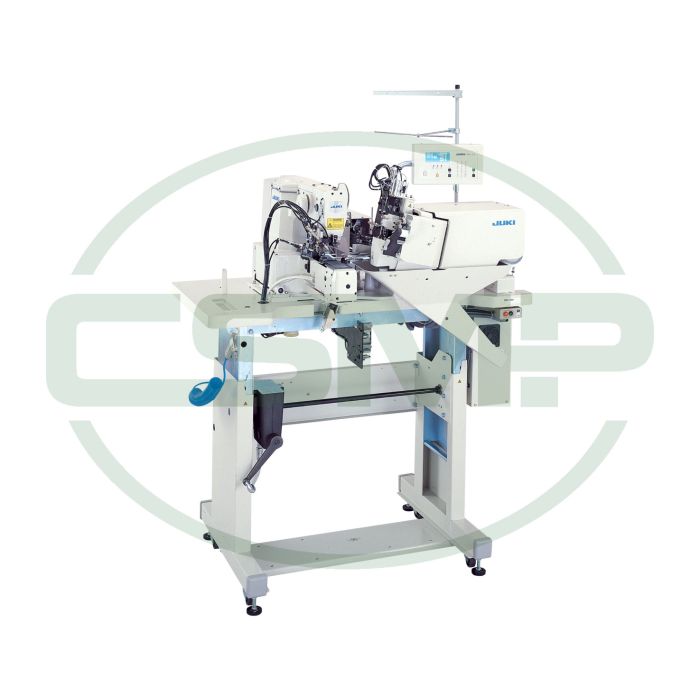
JUKI MOL-254-MABC AUTOMATIC 2 NEEDLE BELT LOOP ATTACHING MACHINE
Description / JUKI MOL-254-MABC AUTOMATIC 2 NEEDLE BELT LOOP ATTACHING MACHINE
Juki MOL-254-MABC
Automatic 2-needle Belt-Loop Attaching Machine
The machine time is 1.2 seconds pre belt-loop, which ensures increased productivity. The feed mechanism incorporates a computer-controlled X-Y method to allow the operator to change the number of stitches and sewing sizes.
The number of stitches and size of bartacking
The number of stitches to sew a belt-loop can be switched between; 28-, 36- and 42-stitches, and the bartacking size can be easily changed through the operating panel. What's more, the user can create his/her own original sewing patterns in addition to the standard ones using JUKI's PGM-20 programming software developed for computer-controlled sewing machines.
The changeover of cutting method between cross cutting and straight cutting
The applicable loop width for the cross-cutting device is increased. In this model, both the cross-cutting device and the straight-cutting device can now cut loop up to 20mm width.
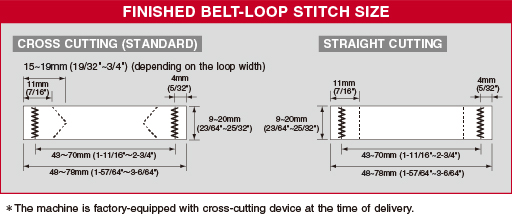
The machine time is 1.2 seconds per belt-loop (with 28 stitches)
The new machine head specifically developed for belt-loop attaching machines runs at a maximum sewing speed of 2,500rpm and is equipped with a direct-drive system that improves start up performance and shortens sewing time. The belt-loop feeding device is now provided with a halfway standby capability for subsequent belt-loops, and its faster belt-loop supply action shortens the time required for supplying belt-loops and helps speed up the machine time to 1.2 seconds per belt-loop (with 28 stitches).
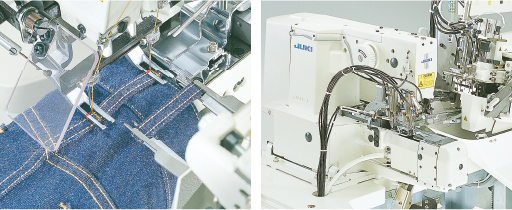
With the improved consistency in belt-loop supply action and re-try capability, the machine down time is substantially reduced
Belt-loops are fed out by the conventional gear-roller feeding mechanism and also drawn out by the new drawing mechanism on the clamp device. Supported by these two mechanisms, the folding fork catches “curled” or “creased” belt-loops every time and supplies them to the head. In addition, the sensor of the clamp device detects the presence/absence of belt-loops. If it detects a faulty belt-loop feed, the clamp device automatically repeats the clamping action. Since the operator doesn't have to operate the set-back switch, less time is lost.
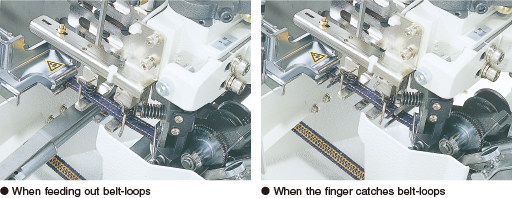
The machine quickly and reliably disposes splices without any delays in cycle time
The machine preliminarily detects each splice in the belt-loops and efficiently disposes them. This means that even when the machine carries out the splice-disposal procedure, the belt-loop feeding device can complete its belt-loop supply action and supply the next belt-loop well before the machine starts to sew. As a result, the operator can perform rhythmical and efficient sewing work with no delay in cycle time. By detecting changes in the material thickness, the machine's potentiometer finds splice in belt-loops and disposes them perfectly.
When changing the material to be sewn, the change in the material thickness recognized by the potentiometer as a splice can be easily adjusted and programmed through the machines's teaching function.
An electric sliding mechanism is installed in the front hook (near the operator)
The newly incorporated electric sliding mechanism is used to electrically shift the front hook when replacing the bobbin or conducting maintenance on nearby components in order to widen the space between the hooks and facilitate the job. In addition, when changing the needle gauge, the front hook can be finely positioned in increments of 0.01mm through the operating panel, thereby allowing the operator to easily adjust the distance between the blade points of the two shuttle hooks. Since the machine no longer requires any adjustment in the hook timing (phase), needle gauge adjustment is much simpler than ever before.
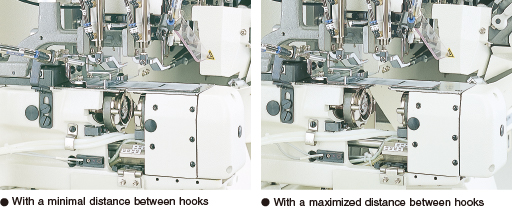
Belt loop supply function
The belt-loop feeding position is automatically adjusted to the belt-loop width. With this capability, the belt-loop width can be easily changed without mechanical adjustment. In addition, when feeding the belt-loop under the presser foot, the widthwise position of the belt-loop can be offset through simple manipulation of the operating panel.
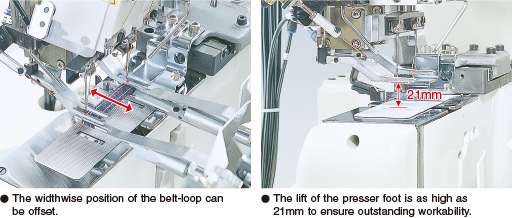
The machine is equipped as standard with an adjustable stand
The height of the working table can be easily adjusted to match the operator's height.
The operator can carry out sewing works in a comfortable posture with less physical strain and fatigue.
Technical Specification
Model name | Juki MOL-254 |
---|---|
Machine head | Computer-controlled, 2-needle, lockstitch bartacking machine |
Max. sewing speed | 2,500sti/min* |
Thread take up | Link type |
Needle bar stroke | 45.7mm |
Thread | Spun thread, cotton thread #50~#30, B33~B46, Nm=120/3~60/3 |
Needle (at the time of delivery) | DP×17 (#21) #19~#21 |
Hook | Horizontal-axis 1.8 fold-capacity shuttle hook |
Lift of the presser foot | 21mm |
Number of stitches | 28, 36, 42 (selectable on the operating panel) |
Needle gauge | 43~70mm (1-11/16"~2-3/4") |
Bartacking length | 7~22mm (9/32"~55/64") ‹adjustable in increments of 0.1mm› |
Bartacking width | 1~3.2mm (3/64"~1/8") ‹adjustable in increments of 0.1mm› |
Number of pieces of bartacking data that can be stored in memory | 9 (99 patterns if optional EP-ROM is added) |
Belt-loop width | 9~20mm (23/64"~25/32") |
Finished length of belt-loop | 48~78mm (1-57/64"~3-5/64") |
Machine time | 1.2 sec./belt-loop (28 stitch) |
Positioning of the front hook | Driven by motor (the distance between the hook can be established in increments of 0.01mm) |
Bobbin winder | Electric type (provided as standard) |
Lubrication | Centralized oil wick lubrication (machine head) |
Lubricating oil | JUKI New Defrix Oil No.2 (equivalent to ISO VG32) |
Power requirement and power consumption | Single-phase, 3-phase 200~240V/350VA |
Compressed air and air consumption | 0.5MPa (5kgf/cm²), 32Nl/min |
Total weight | 230kg |
Dimensions | 1,200mm (W)×800mm (D)×1,350mm (H: in its lowest end) |
Height of the top surface of the throat plate as from the floor surface | 920~1,250mm (provided with the adjustable stand capability) |
*sti/min is the abbreviation for “stitches per minute”
More Information
Part No | JUKIMOL254 |
---|---|
Weight (KG) | 0.100000 |
Manufacturer | Juki |